Could crops fuel future air travel? As the United States works to tackle climate change and reduce carbon emissions, the aviation sector has been targeted for its potential to reach carbon-cutting goals by using renewable fuels.
While renewable fuels like biodiesel, ethanol and renewable diesel have been reducing emissions since the Renewable Fuel Standard was enacted in 2005, sustainable aviation fuel (SAF) is emerging as the most promising path to reach greener skies with the potential to cut carbon emissions by up to 80%.
A large-scale shift from traditional petroleum-based jet fuel to renewable alternatives could drive significant changes in both agriculture and energy, but what will it take to get SAF off the ground? And what could aviation transformation mean for American farmers and fuel producers?
“SAF production is already underway and growth is coming in the foreseeable future, but we’re still in the early stages of adoption,” says Ron Batey, refined fuels pricing and economics director with CHS.
“Widespread change across the aviation industry won’t just require farmers to produce more feedstocks and refiners to process more gallons. Fuel grade standards need to be set, policies that make SAF economically viable need to be shored up and infrastructure needs to be built. Momentum is building, but there’s a long road ahead.”
“As a farmer-owned cooperative with both ag and energy businesses, CHS is uniquely positioned to have a seat at the table and advocate for our owners as opportunities emerge in this new market,” says Darin Hunhoff, executive vice president for energy at CHS.
Push for SAF
Like other segments of the transportation sector, aviation has been identified not just as a key source of greenhouse gas (GHG) emissions — but one that’s expected to grow significantly.
Aviation generates about 2% of worldwide carbon dioxide (CO2) emissions, with U.S. aircraft emissions contributing roughly 24% of that total. As air travel continues to rebound to pre-COVID levels, U.S. jet fuel consumption reached 24 billion gallons in 2023 and is projected to reach 34 billion gallons by 2050. Without efforts to decrease aviation’s carbon footprint, emissions could triple.
But unlike other light- and heavy-duty vehicle markets, solutions like electrification and hydrogen fuel cell technology face steeper hurdles for aviation.
“A key problem with pathways like electrification or hydrogen is that they have low energy density,” says Dave Balzer, senior director, energy economics with CHS. “Carrying a jet tank’s worth of hydrogen or electricity would be too heavy to fly medium or long distances. The best option is to decarbonize the fuel the jet’s engine is already equipped to burn.”
According to the U.S. Department of Energy (DOE), sustainable aviation fuel can be made from a wide range of biological and waste resources, including fats, oils, greases, grains, oilseeds, algae, forestry residues, municipal solid waste and more. SAF has similar properties to conventional jet fuel refined from petroleum, making it a viable “drop-in” fuel that can be blended with conventional jet fuel and is compatible with today’s aircraft technology.
“SAF has gained traction because of its relative near and long-term potential,” says Courtney Hall, senior director of sustainability at CHS. “It’s an alternative that will certainly require innovation but calls more for tweaks within the existing aviation infrastructure than for a drastic build of new systems. It’s an avenue public and private stakeholders eager to cut emissions can start charting the course for today.”
Federal strategy
In 2021, the Biden administration announced the Sustainable Aviation Fuel Grand Challenge, which outlined commitments to target a 20% reduction in aviation emissions by 2030, with production of billion gallons of SAF per year and net-zero aviation emissions by 2050 and the goal of producing 35 billion gallons of SAF per year.
The directive has charted a strategy for the DOE, U.S. Department of Transportation and U.S. Department of Agriculture to collaborate with labs, universities, nongovernmental organizations and stakeholders in aviation, agriculture and energy to accelerate research, development, demonstration and deployment to scale up SAF production.
Additional support was signed into law with the Inflation Reduction Act (IRA) of 2022, which included tax credit incentives for SAF sale and use. The 40B Sustainable Aviation Fuel Credit awards a baseline of $1.25 per gallon of SAF sold or used in a qualified mixture from 2023 to 2024, while the 45Z Clean Fuel Production Credit, which goes into effect Jan. 1, 2025, and sunsets at the end of 2027, will award up to $1.75 per gallon of SAF produced or sold. The IRA also funded $244.5 million in grants to support buildout of SAF infrastructure projects through the Federal Aviation Administration.
“Now the industry has the clearance to innovate, the capital and the government support to fast-track collaboration that will move the needle on SAF,” says Hall.
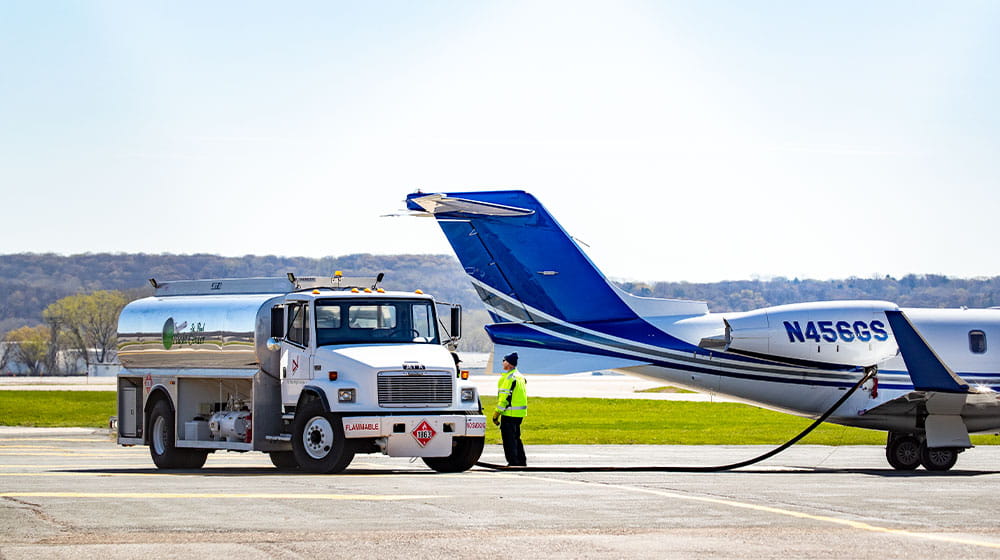
Early momentum
SAF has been used on a small scale for commercial flights for years, but airlines are now making formal commitments to cut emissions. Alaska Airlines has committed to reaching net-zero emissions by 2040 and has an agreement with biofuel company Gevo to purchase 185 million gallons of SAF. Delta has partnered with DG Fuels to purchase 385 million gallons of SAF. United Airlines has announced it will power 50,000 flights with SAF starting in 2028 through its Blue Blade Energy joint venture.
New plants have come online to process SAF, including LanzaJet’s new commercial-scale ethanol-to-SAF biorefinery in Soperton, Ga., and with completion of a new project at Diamond Green Diesel’s plant in Port Arthur, Texas, the facility could upgrade 50% of its current 470-million-gallon annual production capacity to SAF.
Key feedstock-producing states have made early strides to support SAF scaling. Illinois, Minnesota and Washington have implemented their own SAF tax credits. And Minnesota has formed a coalition to build the country’s first SAF hub, using a phased approach to scale production within the state.
“We’re seeing SAF in headlines and, as with any emerging technology, it’s important to see progress, but it’s also important to be transparent about how far adoption has yet to go,” says Hall.
“Only 150 million gallons of SAF per year are being produced worldwide today, and U.S. aviation depends on billions of gallons to power planes,” says Batey. “Today, airlines are blending small amounts of SAF with traditional jet fuel, so SAF accounts for roughly 0.1% of the total fuel used by major airlines. It will be years before production and the logistics required match the headlines we’re seeing today.”
Scaling up production
Government agencies and aviation experts acknowledge goals to build SAF production to a level that could achieve net-zero aviation emissions are ambitious, but scaling SAF to commercial levels is possible.
“The technology that’s processing crude oil or renewable diesel can also be used to produce SAF, and existing renewable diesel plants are making SAF today,” says Batey. “But it’s one thing to produce SAF and another beast entirely to scale it. It all starts with the feedstock.”
The DOE has approved nine pathways to process SAF using a variety of feedstocks, though not all feedstocks hold the same potential for mass production.
Batey notes most SAF in use today is made from used cooking oil and animal fats, but resources to scale with these feedstocks are in short supply.
“Used cooking oil is pretty well tapped out with renewable diesel production. Algae and woody biomass are also approved feedstocks, but the potential to scale production of these resources is limited. Vegetable oils, like soy and canola, and corn via ethanol hold the most potential to scale up to the volumes carbon-cutting goals are aiming for.”
“The feedstocks used for SAF are much more expensive than conventional crude oil,” says Balzer. “The inputs needed to produce a barrel of fuel from crude oil may cost $70, but a barrel using soybean oil will cost around $160. The technology is here, but the equation to produce SAF in an affordable way has not been cracked. Significant subsidies or much higher prices are currently needed to make production financially feasible.”
Grading greenhouse gas impact
The GREET model is a formula used to measure overall greenhouse gas impact of a fuel throughout its entire life cycle. Each fuel type carries a carbon intensity (CI) score, based on geography, resources used in its production and more. Below are some of the factors used to determine a fuel's CI score.

Source: U.S. Department of Energy
Setting feedstock standards
A formal standard for each SAF pathway will be key in determining which feedstocks are most viable for high-volume SAF production.
The Argonne GREET (Greenhouse gases, Regulated Emissions and Energy use in Technologies) model provides a formula that calculates the environmental impact of a fuel through each stage of production and use. Each fuel pathway receives a carbon intensity (CI) score, which reflects the amount of GHG emitted throughout the fuel’s life cycle.
“The GREET model’s CI scores could ultimately pick winners and losers among the pathways and feedstocks that can be used to scale SAF,” says Batey. “A low CI score is needed to take advantage of SAF tax credits. Without those tax credits, it’s not financially feasible to produce SAF.”
The GREET model, first released in 1995, has been updated continually to reflect advanced technology and evolving environmental factors. An expanded version of the model that includes CI scores for key SAF feedstocks was released on April 30, 2024, by the U.S. Department of the Treasury and Internal Revenue Service. The model accounts for emissions produced through the refining process and use of the fuel, plus factors in how and where feedstocks were grown, meaning the same feedstock input could yield a different CI score if grown in Iowa versus in Illinois.
Under new GREET model guidance, traditionally farmed corn-ethanol-to-jet-fuel and canola-to-jet-fuel pathways do not qualify as sustainable aviation fuels due to their CI scores. Fuel producers can reduce a pathway’s CI score by reducing emissions with carbon-cutting methods throughout a fuel’s life cycle, including using lower-carbon grains as feedstocks, although the additional resources needed may pose significant new barriers.
“Take the ethanol-to-SAF pathway, for example,” says Mike Van Houten, senior director for continuous improvement at CHS. “Under the new GREET guidance, ethanol carries a high CI score, but implementing less carbon-intensive growing practices for corn or implementing methods to sequester the carbon produced in ethanol manufacturing can bring the CI score down.
“For fuel producers, the question becomes, what is the reward for being a low- CI producer? How much investment is needed to lower the CI score and earn tax benefits? Is the financial return worth the investment?”
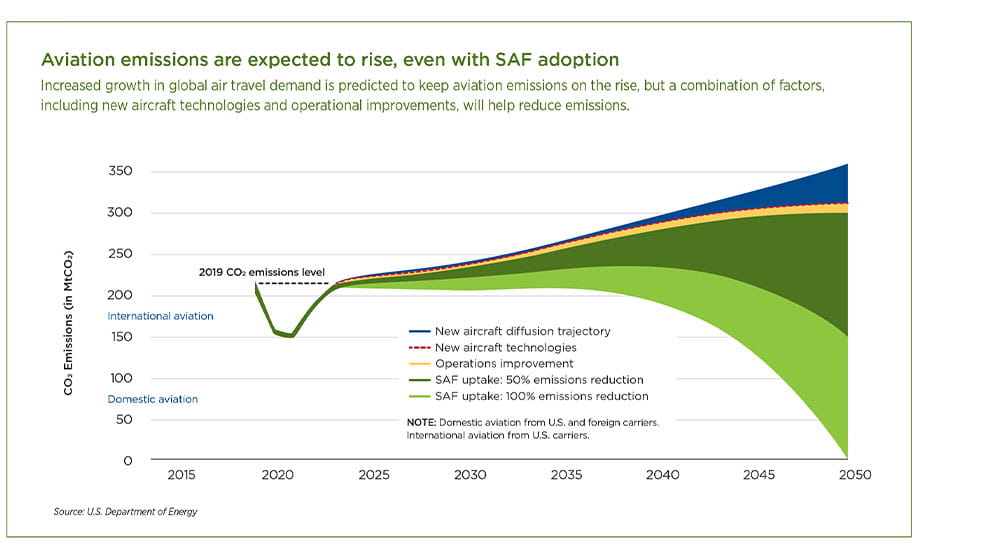
Investing in infrastructure
To reach net-zero aviation emissions by 2050, European SAF supplier SkyNRG estimates the U.S. will need to deploy about 250 SAF refineries, requiring an investment of nearly $400 billion. And, depending on the feedstock used, building new SAF production facilities is likely to pose geographic challenges as additional facilities attempt to align with existing aviation infrastructure.
“SAF produced at a converted crude oil refinery that previously produced conventional jet fuel will likely already have some of the equipment needed and a pipeline directly connected to an airport,” Balzer says. “Building a new stand-alone plant could require building a pipeline to connect fuel with an existing airport, which is no easy feat.”
Geography is also likely to hinder where carbon sequestration would be needed to offset emissions related to SAF production.
“Parts of the U.S. are well-suited to storing CO2 underground, but most fuel processing plants don’t sit in that geography,” says Van Houten. “Those sites would also require the building of pipeline infrastructure.”
Long-term legislation
Legislative policies and programs may play the most pivotal role in getting SAF off the ground.
“Between costly feedstocks and low production volume, SAF is expensive to produce,” says Dan Mauer, Washington representative for CHS. Today, the price of SAF typically falls between two and four times higher than traditional jet fuel.
“No one wants to shoulder that cost while the SAF market matures, and that’s where our federal programs and tax credits come into play. Without policy support at the federal level to offset the cost, fuel producers can’t afford to take the risk and there is no growth for SAF.”
While current legislation provides SAF producers with tax credits for eligible gallons, Mauer notes that these incentives are sunsetting in 2024 and 2027, so will be too short-lived to scale widespread SAF production and reach net-zero emissions goals.
“Today we’re seeing early adopters investing in SAF, but to gain the wide support needed across the industry, stakeholders will need more certainty these credits will be sticking around to invest heavily in production and infrastructure,” says Mauer.
State-level policies could also be key in building momentum and demand for SAF production. In addition to state SAF sales tax incentives, aviation fuels have already been included as “opt-in” fuels under the low carbon fuel standard (LCFS) programs in California, Washington and Oregon, and states that are now building out their own LCFS policies are likely to do the same.
“In coordination with the Renewable Fuel Standard RIN system and state-level tax incentives, revenue from carbon credits linked to state LCFS programs can serve as the third leg of a policy stool that supports SAF growth,” says Dustin Haaland, director of trading and renewable fuels at CHS.
“However, LCFS incentives supporting SAF will likely rely on revenues associated with credits demanded by gasoline and diesel suppliers in that state, rather than jet fuel, since current federal rules prevent states from regulating most jet fuel.”
While the core factors steering a renewable transition in the aviation industry are still taking shape, one thing is certain:
“Like other emerging energy technologies, incorporating SAF into our energy supply chain will be an evolution, not a revolution. Reducing greenhouse gases will rely on a combination of efforts and a mix of liquid fuel solutions will play a role in shaping the SAF market as it matures,” says Hunhoff.
Check out the full Spring 2024 C magazine with this article and more.