When crude oil arrives at a refining facility, its long journey to power businesses and communities across America is just beginning.
After undergoing a complex series of chemical reactions at the refinery, the finished products — gasoline, diesel fuel and propane — will travel hundreds of miles to fuel terminals across the country, ensuring a steady supply of refined fuels is available for delivery to the farmers, cooperatives, retailers and communities who depend on them.
A complex network of CHS pipelines spanning more than 2,000 miles makes it all possible.
Key connector
“Refineries are the heart of our energy production, and pipelines are the vital arteries that keep it all in motion,” says Greg Brown, vice president, pipelines and terminals at CHS.
“Without the pipeline system, crude oil isn’t coming in and finished products aren’t flowing out to reach the customers who rely on them.”
While truck transportation and rail systems are key players in the energy supply chain, Brown says pipelines are critical to quickly, efficiently and safely keeping pace with fuel demand.
“Transportation alternatives move product more slowly, are less energy-efficient and come with much more potential for inherent risk,” Brown says.
Nearly 65,000 barrels of crude oil run through the CHS refinery in Laurel, Mont., each day, while the CHS refinery in McPherson, Kan., runs approximately 115,000 barrels per day. Together, these refineries process roughly 180,000 barrels of crude oil per day — a feat that would require offloading nearly 900 trucks or railcars at the refineries each day without access to pipelines.
“Pipelines are the safest and most efficient way to move energy products and they’re the best equipped to transport the volume of fuel we’re producing,” says Brown.
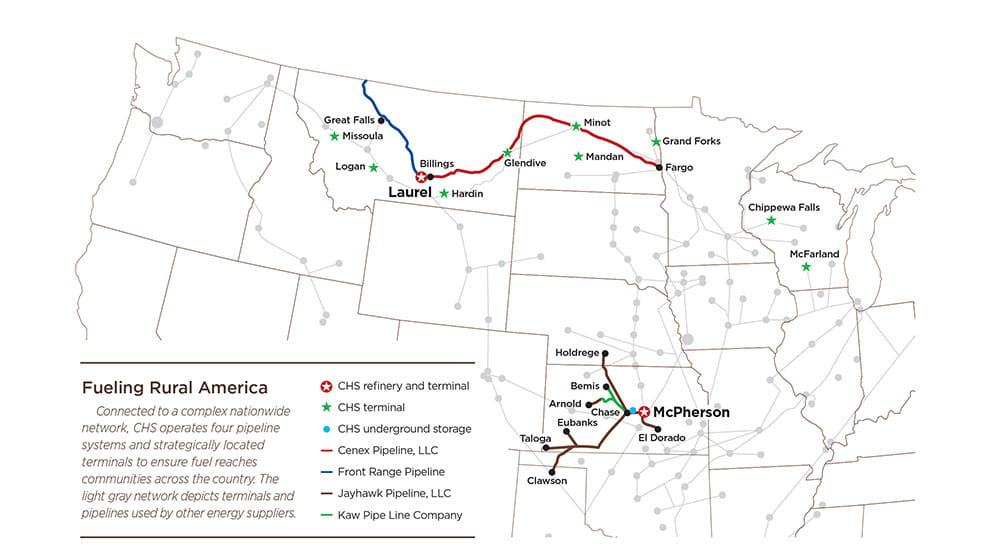
Complex ecosystem
From Montana to North Dakota and from Nebraska to Texas, CHS pipelines transport more than 7,350,000 gallons of crude oil and 2,184,000 gallons of petroleum products per day through four key pipeline systems spanning six states across the western United States. The destination is more than 250 third-party terminals and storage facilities.
Behind the scenes, a team of CHS engineers, technicians and logistics experts keeps fuel products flowing safely and reliably.
“Moving a liquid product from point A to point B sounds simple, but it takes an entire ecosystem of specialists working in sync to keep the system running smoothly,” Brown says.
The process starts with refinery schedulers, who coordinate purchasing crude oil and determine when it will be delivered to the refinery via pipeline. Once the crude has been processed and refined into gasoline, diesel and propane, pipeline schedulers manage incoming bids from shippers, analyze storage levels and assign delivery routes to ensure the correct volumes of fuel reach their intended destinations.
As routes are assigned and fuels are pumped through the pipeline web to terminals across the country, terminal operators coordinate truck deliveries to the fuel’s final destination, from retail wholesalers to storage tanks at cooperatives, farms and ranches.
As fuels travel through the pipeline system, the operations team monitors liquid flow rate, as well as performance at each station along the way, to ensure pumps are functioning correctly and product is moving as it should.
Throughout the year, engineers run tests to ensure pipeline performance meets federal and state compliance standards, while the maintenance team handles regular inspections along the pipeline system and makes necessary repairs.
“To keep fuel moving without disruption, teams need to work together like a well-oiled machine,” says Brown. “Coordination across the full system is what keeps CHS owners and customers connected to a reliable fuel supply.”
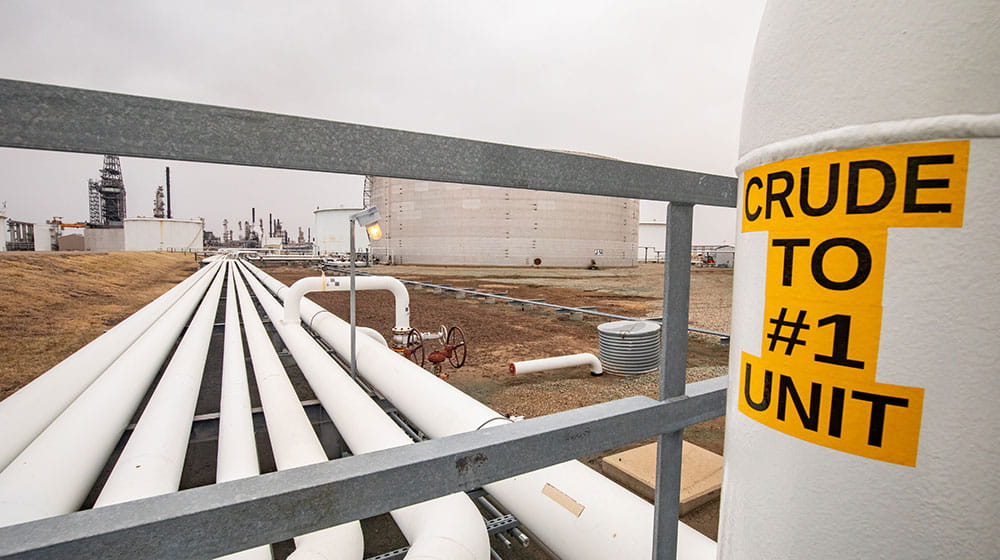
The Jayhawk Pipeline carries crude oil to the CHS refinery in McPherson, Kan.
Investing in infrastructure
Regular pipeline maintenance and repair are vital to ensure crude oil and refined fuel products are delivered safely and reliably.
From internal inspections and analyses to excavations and pipe replacements, senior reliability engineer Matt Rinkenbaugh and the operations team use high-tech procedures to monitor CHS pipeline systems, upgrade existing infrastructure and prevent issues before they arise.
With the help of a pipeline inspection gauge — commonly known as a smart PIG — Rinkenbaugh and his team can see inside the pipeline. Smart PIGs can detect corrosion, metal loss, small cracks and dents, and other threats to the pipeline’s integrity.
“As we inspect and make repairs, we also have an opportunity to invest in the infrastructure,” Rinkenbaugh says. “Most pipelines are made from carbon steel, but we’ve seen a lot of advancements in manufacturing and technology through the years. As we go in to complete a cutout or pipe replacement, we install materials that have been engineered to be less susceptible to integrity issues for safer operation.”
Rinkenbaugh notes CHS pipeline maintenance schedules are more stringent than federal and state regulations due to a focus on safety and reducing risk.
“Federal guidelines only set the strictest standards for select locations deemed to be high-consequence areas, which are usually near highly populated areas, drinking water or wildlife preserves,” Rinkenbaugh says.
“At CHS, we approach any territory our pipes touch as a high-consequence area and treat each pipe as if it’s running directly through our owners’ yards. An investment in infrastructure maintenance is an investment in their safety.”
An ultrasonic smart PIG launched from Phillipsburg, Kan., will travel more than 100 miles at 1.5 miles per hour, gathering data from inside the pipeline, before it reaches its final destination at the CHS station in Chase, Kan.
Anatomy of a smart PIG
Pipeline operators use pipeline inspection gauge tools — often referred to as smart PIGs — to track and understand what’s happening inside the pipe.
These computer-based systems can be used to clean out a pipe or locate potential obstructions within the pipe, while others use a variety of technologies to analyze the physical state of the pipe.
Magnetic flux leakage PIGs use magnets to detect potential metal loss and corrosion in the pipe. Caliper tools use finger-like features to detect possible dents in the pipe, and ultrasonic inspection PIGs work like sonar to create and reflect sound waves in a pipe to detect possible cracks.
While PIGs travel through each pipe, they collect data that the CHS team analyzes to determine where maintenance and repairs may be needed and to flag potential safety risks.
“These high-tech tools are tracking and scanning as they go, allowing us to see through our steel pipes and catch issues before they happen,” says Matt Rinkenbaugh, senior reliability engineer for CHS.
A team of engineers, welders and mechanics coordinates with the pipeline control room team to prepare pipelines for inspections, maintenance and repairs.
Building community partners
CHS maintains close relationships with local first responders, industry associations and community organizations to share safety information, resources and training opportunities.
“Maintaining a strong working relationship with the communities our pipelines cross is critical, especially in an emergency,” says Enden Nelson, who leads public awareness efforts for CHS pipelines.
“We’re able to detect potential incidents and isolate sections of our pipeline remotely from our control rooms, but we operate a network that spans thousands of miles, so if an emergency occurs, local responders may be nearest to the scene. We work closely with community partners to ensure they’re as prepared as our own team to respond when needed.”
The CHS pipelines team meets regularly with local emergency planning committees and works in tandem with state pipeline associations, circulates pipeline safety information to communities and landowners, and runs tabletop exercises and drills with community partners to practice emergency preparedness response strategies.
“The time to prepare for an emergency is not after it’s happened,” says Jake Hover, a pipeline environmental engineer with CHS. “We invest in training for groups like local fire departments and local law enforcement so we know they’re set up for success and we’re all operating off the same playbook.”
Hover notes CHS training efforts are particularly impactful in rural communities, where local fire departments are often staffed by volunteers with high turnover rates.
“Sometimes the folks you’ve trained are gone in a year or two, so efforts to keep an open line of communication with community partners don’t just build relationships, they also ensure our new partners stay up to speed.”
Designed to deliver
The pipeline infrastructure will remain a critical asset in the energy supply chain for years to come.
“As a cooperative-run refinery, our focus is centered on meeting the needs of our owners and customers. Pipelines play a vital role in creating the connections that power producers and rural communities across America,” says Brown.
“The investments we’re making today to maintain and protect our pipelines and the communities they are part of will allow us to deliver a steady, safe supply of fuel to our owners well into the future.”
Play it safe
More than 100 billion feet of underground utilities and enough pipeline to wrap around the equator 88 times lie under U.S. soil.
When starting any soil-related project, call the 811 Call Before You Dig line — a free service that helps locate and mark pipelines in your area — to keep you and your operation safe. Consider these tips before digging:
- Any soil-related project deserves a call: Whether you’re building a waterway, digging fencepost holes or subsoiling, check with 811 before starting a project that breaks ground.
- Each project is a fresh start: Depth of pipelines and utility lines can change over time due to erosion, frost and thaw, and other ecological activities. Don’t assume you know where utilities are located.
- Depth isn’t a disqualifier: Many utilities are less than a foot underground. Better to be safe than sorry and call 811, even before small projects.
- One call can save you time and money: 811 is a free service and making a quick call can significantly reduce your potential liability for costly damages to your operation. All work to mark utilities is done by professional locators and covered by utility companies.
Learn more: Call 811 or visit call811.com before you dig.
Check out the full Spring 2025 C magazine with this article and more.
Find pipelines near you.